Stability chambers – what is stability testing?
In the pharmaceutical industry, stability testing is used to evaluate how a drug or medicinal product will be affected by different environmental conditions over time. This is a regulatory requirement for bringing new products to market. Stability testing allows pharmaceutical companies to expose the product to conditions that might occur throughout the supply chain e.g., temperature, humidity, and light exposure, as these conditions may cause a drug to degrade or lose efficacy. Stability test chambers can also be used for accelerated ageing studies and to determine the shelf-life and expiration date of products. Stability testing is not just used for chemical pharmaceuticals, but also for biological products such as proteins, polypeptides and conjugates.
What are the guidelines for stability testing?
The guidelines for stability testing are outlined by the International Council for Harmonisation of Technical Requirements for Pharmaceuticals for Human Use (ICH) (Topics Q1A – Q1F). Stability chambers are specialised incubators that can be programmed to mimic environmental conditions. A batch of drug products can be placed inside a stability chamber for a selected time period (e.g., one month / one year) and analysed periodically to assess the impact on quality. The guidelines set out by ICH are highly specific with allowable temperature deviations of only 2-3°C and humidity deviations of ≤5%. In order to ensure these conditions are maintained over long periods, high-performance stability chambers must be used.
Important questions when choosing a stability chamber
- Can the chamber consistently maintain the environmental conditions?
- What is the uniformity of the conditions within the chamber?
- What kind of air flow is used in the chamber?
- What is the accuracy of the temperature and humidity sensors?
- How many programs / segments do I need?
- Is data available on the long-term performance of the chamber?
- Does the chamber have alarms for temperature/humidity deviations?
- Are the records 21 CFR Part 11 compliant?
- Can the chamber be monitored remotely?
- Are internal surfaces easy to clean?
MMM CLIMACELL Environmental Chambers
CLIMACELL from MMM are environmental chambers with patented forced air circulation, cooling, and controlled humidity. Available in a range of volumes from 111 to 1212 litres with a temperature range from -20°C to 100°C.
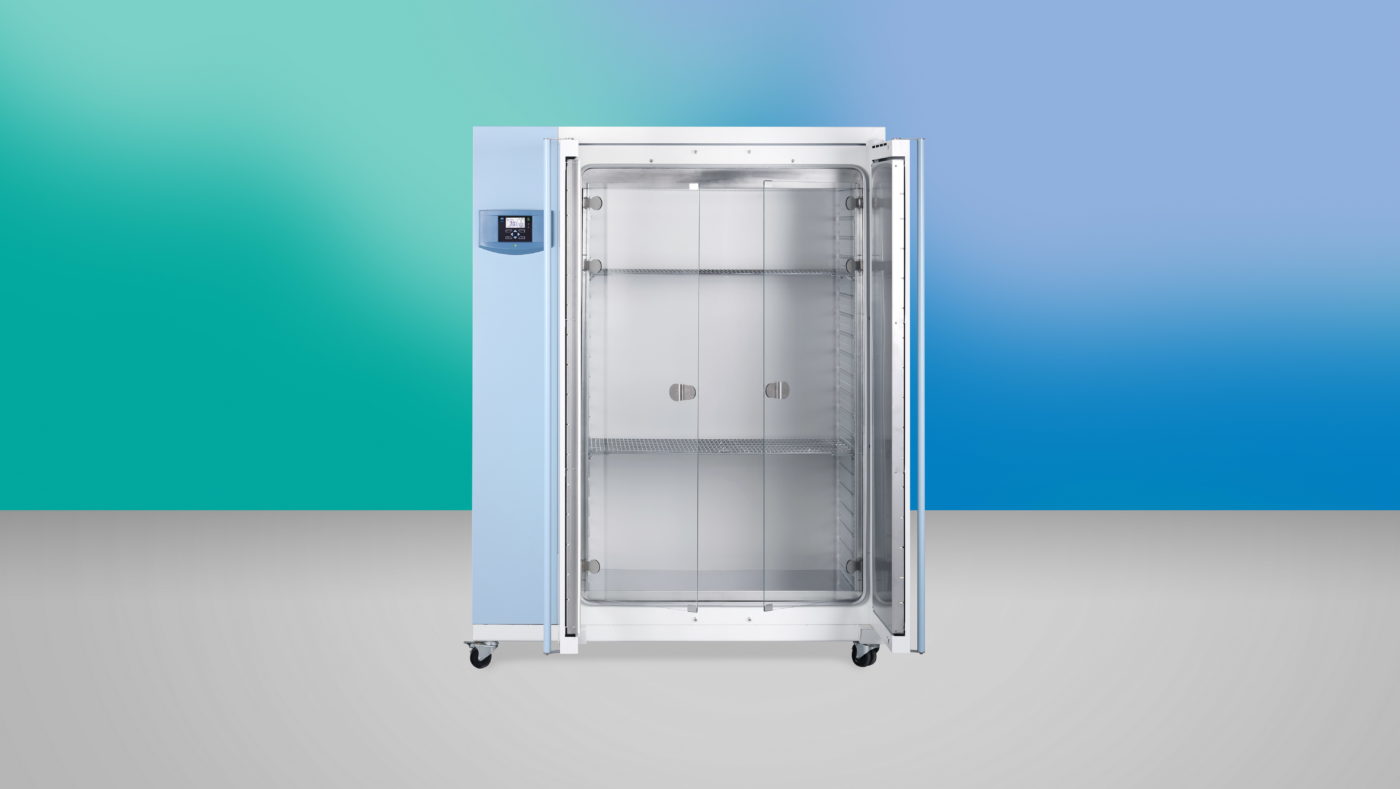
Programmable Exposure Lighting
The CLIMACELL range offers a wide selection of lighting configurations:
- Fluorescent tubes in the door – up to 36,000 lux
- Fluorescent tubes in shelves – up to 23,000 lux
- LED lighting in the door – up to 21,000 lux
- White LED lighting in shelves – up to 30,000 lux
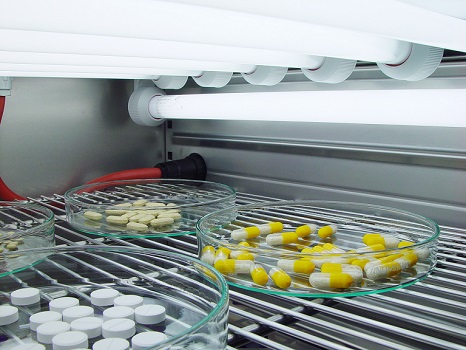
Accurate Temperature Control
- Operating temp: -20°C to 100°C
- Temp deviation in space (37°C): <1°C
- Temp deviation over time: <0.4°C
- Recovery time after 30 second door opening: <6 min to 37°C
Tight Humidity Control
CLIMACELL chambers maintain relative humidity at the selected value with <2% deviation over time. In order to ensure accurate, long-term regulation of humidity, the steam generator of CLIMACELL® should be used with demineralised (DI) water only. DI water can be supplied in two ways.
- Filling a 5L DI water barrel (delivered with unit) and connecting to the device pump
- Connecting the CLIMACELL directly to the building’s DI water distribution system
In both cases, the device automatically takes the exact quantity of water required for humidity regulation to the internal steam generator.
Optional Accessories
Thanks to the modular design of CLIMACELL, it can be additionally equipped for testing of photo-stability, simulation of day and night, processes with CO2 control and hot-air decontamination.
Hot air decontamination 160°C | Access ports Ø 25, 50, 100 mm |
Additional cooling −20°C | Programmable inner sockets |
Defrosting system | External printer |
CO2 control | Multi-level administration of users |
WarmComm 4.0 Monitoring Software | FDA 21 Part 11 compatible data logger |
Data module USB device, Ethernet, Wi-Fi | Up to 100 programmes – 100 segments each |
Mechanical/electromagnetic door locks | BMS relay volt-free alarm contact |
For more information on the CLIMACELL range, please get in touch below:
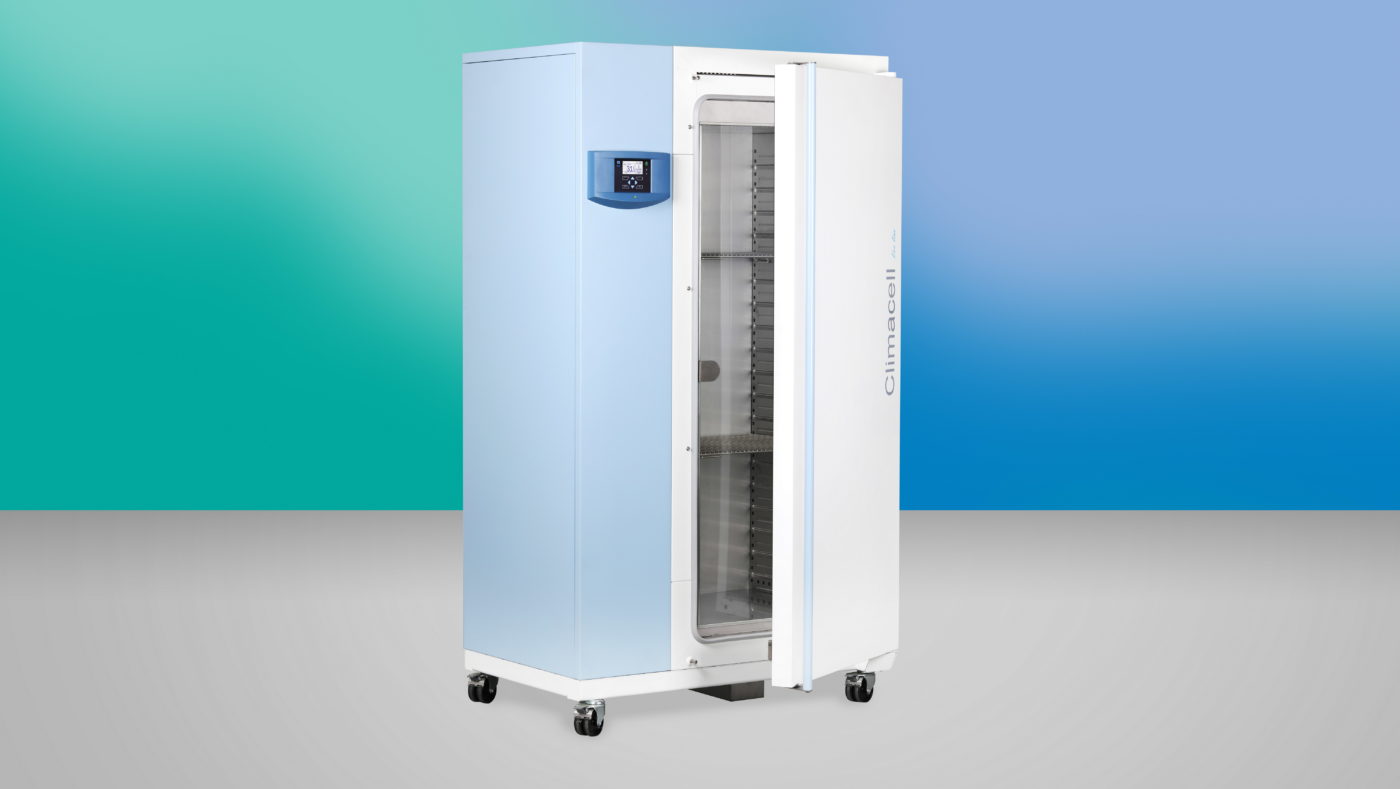
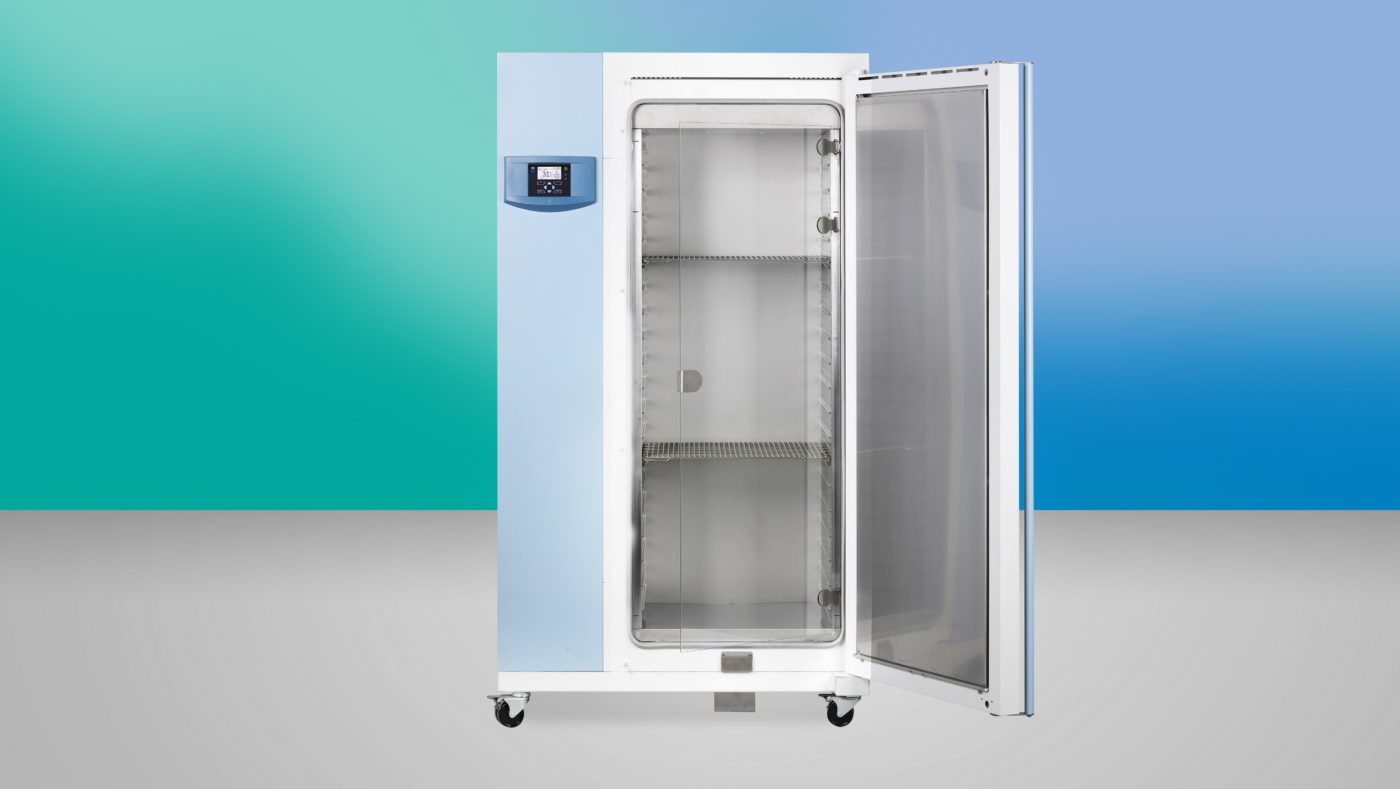